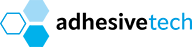
Achieving optimal results with epoxy applications hinges on precision and understanding of these critical processes.
Dispensing
Dispensing
Most problems related to curing epoxy can be traced back to inadequate mixing or the incorrect ratio of resin and hardener. We recommend using WEST SYSTEM calibrated pumps to dispense resin and hardener for simplified metering. WEST SYSTEM pumps are calibrated to dispense the correct working ratio for all WEST SYSTEM and some ADR Range liquid resin and hardener combinations.
Before using the first mixture on a project, ensure the pumps deliver the correct ratio. Refer to the verification procedure outlined in the pump instructions. Check the ratio regularly or whenever curing issues arise. Production facilities should routinely verify pump ratios.
For weight or volume measurements, consult the Adtech’s Technical Data Sheets for the accurate resin-to-hardener ratio.
Pot Life
Pot Life
The length of a resin and hardener combination’s pot life may be a factor in its selection. Pot life is a term used to compare the relative rate of reaction or cure speed of various resin/hardener combinations. By definition, it is the time a given mass of mixed resin/hardener will remain in the liquid state at a specific temperature.
To compare pot life, we determine the pot life of an individual resin/hardener combination based on a 100 or 500-gram mixture in a standardized container at a consistent temperature. Pot life does not directly correlate to actual working life or assembly time but indicates the potential working time of a resin/hardener combination relative to others. The actual working life of an epoxy mixture is influenced by its mass and temperature during the manufacturing or assembly process. For more information on controlling cure time, please refer to the section “Controlling Cure Time.”
Mixing
Mixing
To achieve error-free results when mixing epoxy, follow these three steps:
- Dispense the correct proportions of resin and hardener into a clean plastic or paper mixing container. Avoid using glass or foam containers due to the risk of heat build-up. Start with a small batch if you are unsure of the epoxy’s pot life or working time.
- Thoroughly stir the two ingredients together until they are uniformly blended. Scrape the sides, bottom, and corners of the container while mixing. If using a power mixer, ensure you scrape the sides and corners. Operate the mixer slowly to prevent air from being stirred into the epoxy mixture. Consider dyeing the resin and hardener for better blending.
- After mixing, transfer the resin and hardener mixture to a roller pan, impregnator, or part immediately to maximize working time. If pigments or fillers are added, stir them thoroughly before transferring the mixture. Be cautious of the heat generated during the curing process. A plastic container filled with mixed epoxy can melt if left unattended. If an uncontrolled exotherm occurs, move the mixture to a well-ventilated area immediately. Do not dispose of any epoxy until the reaction has cooled.
Curing
Curing
The transition period of an epoxy mixture from a liquid to a solid is known as the cure time, which consists of three phases: working time (liquid state), initial cure (gel state), and final cure (solid-state). The duration of each phase and the total cure time depend on the ambient temperature.
Working Time refers to the period after mixing when the epoxy remains liquid and workable. It is crucial to apply clamping pressure to achieve a reliable bond before the epoxy starts to cure.
Initial Cure Phase once the working time ends, the mixture enters the initial cure phase, reaching a gel state. While it may be firm enough for shaping with tools, it is too soft for dry sanding. During this phase, post-cure heating can begin.
Final Cure Phase during the final cure phase, the epoxy mixture solidifies. Without post-curing, it continues to cure at room temperature over a few weeks. Post-curing at elevated temperatures accelerates the final cure phase, especially for components requiring optimal thermal properties.
Controlling Cure Time
Controlling Cure Time
Several factors affect cure time and can be manipulated to extend the length of the cure time and working time:
1. Type of Hardener:
Each resin/hardener combination will undergo the same cure phases but at different rates. Choose the hardener that gives you adequate working time for your job at the temperature and conditions you are working under. PRO-SET® Hardeners may also be blended to provide a custom blend with an intermediate cure time. Refer to the blend profile charts in the Laminating Epoxies and Infusion Epoxies sections.
2. Mixed Quantity:
Mixing resin and hardener together creates an exothermic (heat-producing) reaction. A larger quantity of mixed epoxy generates more heat and yields a shorter working time and overall cure time. Smaller batches of epoxy generate less heat than larger batches and have longer cure times. Therefore, a thicker joint, thicker laminate, or layer of epoxy will cure quicker than a thin layer.
3. Container Shape:
Heat generated by a given quantity of epoxy can be dissipated by pouring the mixture into a container with a greater surface area (a roller pan, for example), thereby extending the working time. Since the mixed epoxy will cure faster while it’s in the mixing container, the sooner the mixture is transferred or applied, the more the mixture’s working time will be available for assembly.
4. Temperature:
Heat can be applied to or removed from the epoxy to shorten or extend working and cure times. This can be especially beneficial when assembling large or complicated components requiring maximum working time and minimum final cure time. Before implementing these techniques, ensure you fully understand the effects of heating and cooling on the mold.
Before mixing, moderate heat can be applied to the resin and hardener to shorten the epoxy’s working time. Conversely, a cooler box can draw heat from a roller pan to extend the working time. For larger operations, impregnating machines with water-cooled rollers are available to extend working time.
After the epoxy is applied, a fan can draw heat from the process or application and extend the epoxy’s working time. The tooling can be designed to extend working time and shorten cure time.
It is possible to build tooling with tubing embedded. During processing, cool water pumped through the mold draws heat from the part, extending the working time. When the process is complete, hot water or steam pumped through the mold will speed the cure of the part. Moderate heat (hot air gun or heat lamp) applied to the assembly will shorten the epoxy’s cure time. Heat can be applied as soon as the assembly is completed, but most often heat should be applied after the epoxy has reached its initial cure. Heating epoxy that has not reached its initial cure will lower its viscosity, causing the epoxy to run or sag on vertical surfaces. In some processing procedures, heating too soon can lower the resin content of the laminate to unacceptable levels. In addition, heating parts that contain porous materials (wood or low-density core material) can cause the substrate to “out-gas.” When the air in the porous material expands and passes through the curing epoxy, it can leave bubbles or pinholes in the cured epoxy.
Shelf Life & Storage
Shelf Life & Stroage
Epoxy resin and hardener formulations have longer shelf lives than many polymers. The standard infusion and laminating epoxies have a minimum shelf life of three years for resins and two years for hardeners. We recommend visually inspecting and stirring the resin as needed.
To maintain the quality of PRO-SET® Epoxy resins and hardeners, store them at room temperature (65°F-85°F, 18°C-29°C) in sealed containers until shortly before use. Exposure to low temperatures during storage (<55°F, <12°C) may cause the resin to crystallize, especially if containers are placed near outside walls or on the floor where temperatures may be lower than ambient conditions.
In case of crystallization, warm the resin to 125°F (51°C) for eight hours and stir to dissolve crystals. To prevent hardeners from forming carbamation, keep containers sealed and pump reservoirs covered until just before processing. Exposure to CO2 and moisture in the atmosphere over extended periods can lead to carbamation.